I was able to finish off two brushes today. Worked on cleaning out the knots on 3 other ones today. It was a bit of a learning process and I definitely will do a few things differently on the other ones. I got in a TGN Finest F2 in 20mm and their 3 band synthetic in 20mm. The Vic Shaving (Virginia Sheng) knot new synthetic arrived today from China - pretty darn quick - like 10 days, so figured should get to work.
I received this Sanax nylon brush in the mail today too - it was a first generation synthetic so wanted to re-knot it with a synthetic. Used a small drill bit for a pilot hole after cutting off the knot. I used painters masking tape to protect the handle when I was drilling and removing the knot. After the pilot hole was drilled - I then used a wood drill bit for getting the majority of the knot base. Then used the dremel and small drill bits and small sanding drums to get the hole prepared.
After the old knot was out and the hole was about the right size - then went about removing the painters tape and started using wet sanding paper 600, 1000, 1500, 2000, 2500 to clean up the handle. There was a line where the plastic handle was poured - used the dremel with fine grinding bit to take that down and then smoothed it all out. After the wet sand - cleaned it up with 3 applications of Flitz polish and a microfleece cloth.
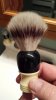
I used the TGN synthetic 3 band knot in this one - as it seemed to splay a little better - both were soft on the face, good backbone - but this one seemed to be easier to spread out on face - at least with less pressure.
This Sanax handle had a sub-floor in it - where the ivory section was - where the dark blue top ends. It had pretty decent weight to it. Here is my screw up - I should have used cork or something else to build up the base to where the knot would be. Instead - I pretty much filled the cavity up with epoxy. I was thinking it would add some additional weight - but it should be lower. I got a little lucky and guesstimated right on the amount and the knot depth and ended up epoxying the knot right in. One of my kids made off with my metal ruler with CM's on it - I think that it is set at 51-52mm of loft if my measurements were right.
The next brush is a Ever Ready 100 ivory handle. I used the TGN finest F2 in it - it is also set at 51-52mm which is not ideal - probably should have set it deeper 47mm or so - but it just didn't look right to me visually. May very well regret that after it blooms out.
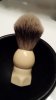
Had sanded this last week - so just hit this with some Flitz polish and checked the knot hole to see if it would fit. I used 00 buckshot - I believe 8 pellets mixed with some 30 min epoxy to add weight at the base. When the epoxy set up for about an hour - I did not want to make the mistake of filling up the rest of the bulb with epoxy, so measured and cut a wine cork to provide a filler. I used a bit of epoxy to put the cork in, then at the top of it - put a little epoxy on top of the cork. The epoxy was a little sloppy and I see some of it had creeped up just a bit on the knot in a couple of spots - you can see it - not a lot, but I know it is there.
Waiting to let the epoxy to really set up overnight before testing them out. Here is a view of the two from the top:

I have a best badger knot, a finest and a pure badger knot on the way for some other handles (Ever Ready C40, Ever Ready 100 and Made Rite pure badger). I will need to pay more attention to epoxy and weighting of the handles. Need to measure a bit better to make sure that I am putting the knot at the right loft.
Hopefully they will work out well.
I received this Sanax nylon brush in the mail today too - it was a first generation synthetic so wanted to re-knot it with a synthetic. Used a small drill bit for a pilot hole after cutting off the knot. I used painters masking tape to protect the handle when I was drilling and removing the knot. After the pilot hole was drilled - I then used a wood drill bit for getting the majority of the knot base. Then used the dremel and small drill bits and small sanding drums to get the hole prepared.
After the old knot was out and the hole was about the right size - then went about removing the painters tape and started using wet sanding paper 600, 1000, 1500, 2000, 2500 to clean up the handle. There was a line where the plastic handle was poured - used the dremel with fine grinding bit to take that down and then smoothed it all out. After the wet sand - cleaned it up with 3 applications of Flitz polish and a microfleece cloth.
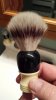
I used the TGN synthetic 3 band knot in this one - as it seemed to splay a little better - both were soft on the face, good backbone - but this one seemed to be easier to spread out on face - at least with less pressure.
This Sanax handle had a sub-floor in it - where the ivory section was - where the dark blue top ends. It had pretty decent weight to it. Here is my screw up - I should have used cork or something else to build up the base to where the knot would be. Instead - I pretty much filled the cavity up with epoxy. I was thinking it would add some additional weight - but it should be lower. I got a little lucky and guesstimated right on the amount and the knot depth and ended up epoxying the knot right in. One of my kids made off with my metal ruler with CM's on it - I think that it is set at 51-52mm of loft if my measurements were right.
The next brush is a Ever Ready 100 ivory handle. I used the TGN finest F2 in it - it is also set at 51-52mm which is not ideal - probably should have set it deeper 47mm or so - but it just didn't look right to me visually. May very well regret that after it blooms out.
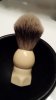
Had sanded this last week - so just hit this with some Flitz polish and checked the knot hole to see if it would fit. I used 00 buckshot - I believe 8 pellets mixed with some 30 min epoxy to add weight at the base. When the epoxy set up for about an hour - I did not want to make the mistake of filling up the rest of the bulb with epoxy, so measured and cut a wine cork to provide a filler. I used a bit of epoxy to put the cork in, then at the top of it - put a little epoxy on top of the cork. The epoxy was a little sloppy and I see some of it had creeped up just a bit on the knot in a couple of spots - you can see it - not a lot, but I know it is there.
Waiting to let the epoxy to really set up overnight before testing them out. Here is a view of the two from the top:

I have a best badger knot, a finest and a pure badger knot on the way for some other handles (Ever Ready C40, Ever Ready 100 and Made Rite pure badger). I will need to pay more attention to epoxy and weighting of the handles. Need to measure a bit better to make sure that I am putting the knot at the right loft.
Hopefully they will work out well.